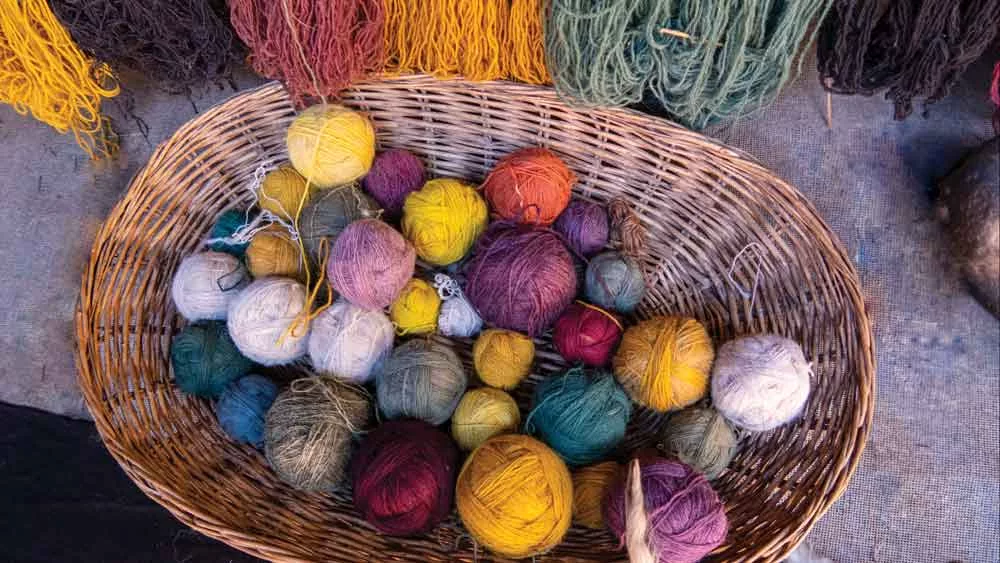
But there may be hope on the horizon, as a renewed interest in wool seems to be on the rise and a local organization is stepping in to help.
Throughout the North Bay wool producers and artisans had been noticing a growing interest in natural fibers and fiber arts even before the pandemic kept us at home and looking for things to occupy our time. Classes in knitting, weaving, felting and natural dyeing have become more popular and are happening in yarn shops, farms and living rooms.
Part of that interest may lie in a growing awareness about so-called “forever chemicals” in plastics and increasing misinformation about the feasibility of plastics recycling. Matt Simon, a reporter for Wired and author of “A Poison Like No Other: How Microplastics Corrupted Our Planet and Our Bodies,” has written about how the garment industry has been exposed for polluting water, air and even our bodies with synthetic fiber textiles that break down into toxic microplastics.
In 2010, Rebecca Burgess launched the North Bay nonprofit Fibershed to address concerns with the garment industry and its polluting synthetics. Similar to a local watershed, the name implies a regional focus on stewardship that’s often informed by the wisdom of local indigenous practices.
Like the slow food movement, the idea is that no harm should be done to the local environment, people or animals by the production and use of the fibers. This begins with the health of the soil and runs all the way through the production and use of the fiber until it’s returned back to the soil again where it can be composted.
The Fibershed movement has been steadily growing, and its Producer Program now hosts around 180 member farmers, ranchers, designers, sewers, weavers, knitters, felters, spinners, mill owners and natural dyers from 51 counties in the North and Central regions of California.
Heather Podoll, Fibershed’s partnership and advocacy coordinator, is among 70 members in the North Bay working to build infrastructure, community connections, market development and “just basic skill” to promote textile production.
“The benefits of a system like that are that we lower the overall footprint of our textiles when we’re producing them and consuming them and taking care of them within a smaller geographic area close to where we live,” Podoll says.
This includes the ability to get the wool to a mill to be processed. Currently there are four wool processing mills that are members of the Northern California Fibershed Producer Program network: Mendocino Wool and Fiber, Valley Oak Wool Mill in Woodland, Huston Textile Company in Sacramento and Woolgatherer Carding Mill in Montague.
Fibershed textiles are made without any toxic additives—and when the wool is dyed it’s done using natural dyes from the region. Fibershed hosts classes at its Learning Center in Point Reyes Station where members grow dye plants and teach natural dyeing techniques. They also host events where members can bring products to sell.
“So, for a Fibershed-certified product within our community, you’re looking at something that’s been grown, produced, designed, manufactured and dyed from the community and from the local environment,” Podoll says.
Fibershed is emphasizing that microplastics are largely coming from synthetic textiles and clothing. Garment industry marketing has promoted that the industry’s practices are environmentally safe, but natural-fiber proponents say they’re “greenwashing” the reality of the situation.
Podoll, for instance, notes that the textile industry has been incredibly successful in promoting the growth of both recycled and virgin polyester—despite studies having revealed that recycling plastics results in large amounts of microplastics being released into the air.
Microplastics are released from synthetic-fiber clothing even as they are worn. And, unlike natural fibers, synthetic-fiber clothing needs to be washed regularly—which is when the most microplastics are released from those garments.
Podoll says Fibershed is advocating for lower consumption of clothes overall and making use of natural fibers which are not made from fossilized carbon.
“Wool and silk have much longer life spans in someone’s closet and they tend to require less-frequent washing,” Podoll says. “Wool is naturally odor and stain resistant and has these wonderful temperature regulating qualities that make it very comfortable to wear in a lot of different conditions,” she says. “The structure of the wool fibers is very unique.”
Podoll points out that since wool has that longevity it’s worth investing time into mending wool garments. Fibershed hosts monthly mending workshops at its Learning Center and Podoll says they’re very popular. She says she’s hearing of a lot of local interest in mending and improving the longevity of clothes.
“I think a lot of people have wool garments that they’re willing to invest some time in—patching up a hole or kind of making something new again that they know could have a long, long life,” she says. “If they get that elbow patched up or some little holes or tears that have come up, wool garments can really last for decades.”
Preaching to the flock
Hazel Flett wears wool to keep warm when she’s bringing in the sheep at Bodega Pastures where the cool ocean air ushers a chill to the rolling hills of west Sonoma County. “Natural fibers are so much better,” Flett says. “They’re healthier, they’re warmer. I love to knit, so I suppose because I work with natural fibers all the time I’m not drawn to working with synthetics.”
Flett has been living and working at Bodega Pastures since 1979 and helps raise a couple hundred sheep on the 1,000 acre ranch. They keep a mixed flock of Corriedale, Romney, Suffolk, Navajo-Churro, and Dorper sheep, allowing for a variety of textures and qualities that are useful for felters, spinners, knitters and weavers.
Flett also helps with classes at Bodega Pastures—offering sessions in things like choosing a fleece, shearing, washing a fleece, natural dyeing, spinning and felting.
Like all Fibershed members they are stewards of the land, using regenerative agricultural practices that help make the ranch sustainable. Flett notes that everyone at Bodega Pastures enjoys the sheep. She knows them all, as well as their personalities, histories and even their lambs. “They’re very used to people,” she says.
Flett says that sheep must be sheared for their health and comfort. She says a good shearer doesn’t hurt them. “He or she spends 2 or 3 minutes getting all that weight of wool, around 7 pounds, off them and the sheep is then up and back on pasture, and is much more comfortable for the summer,” Flett says. “A new coat starts to grow and the sheep is well covered by winter.”
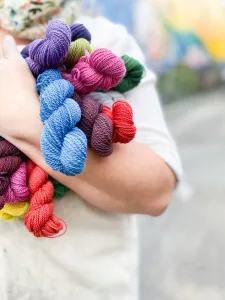
“The unlucky sheep is one who gets missed and is carrying all that weight,” Flett says. “In winter it can get waterlogged and she’d have trouble getting up.”
They send the wool to a mill to be washed and turned into products like raw fleeces, yarn, roving and batting. Flett notes that Fibershed has been working to bring a mill closer to the area to make it easier for local wool producers.
A lot of their wool gets turned into yarn. “I knit some of that up and sell it as hats, socks and whatnot,” Flett says. “We sell a lot of those over the winter.”
They sell yarn at the Artisan’s Coop in Bodega and Flett takes the yarn and other products to local farmers markets when the weather permits. “Sebastopol has a year-round market, and I’m there most weeks, unless it’s raining,” she says. “This winter has been something else. I missed a lot of markets.”
When she’s at the markets, Flett is noticing that more people seem to be interested in wool products and are asking questions about it. “A lot of people say they wish they knew how to knit,” Flett says. “I should be doing more teaching than I am because obviously sales are dependent on people being able to do something with the wool.”
Dyed in the wool
In Napa County, a Fibershed member has helped make sure that local wool is being used. Twenty years ago, Brooke Sinnes learned that Napa farmers were throwing away, composting or just stashing wool in their barns. This was because the price per pound was so low that they lost money when sending it out to be processed into yarn and roving.
Sinnes considered this a travesty and decided to do something about it. She began buying small batches of local wool at a higher price and sending it to a mill near Davis. She’d get the wool back in yarn and roving and then dye it with natural dyes, increasing its value before selling it.
Her business, Sincere Sheep has been going strong for two decades now and she’s increased the amount of wool she’s buying. She’s helping lots of Napa Valley farmers and ensuring that their wool doesn’t get thrown out or stashed away in the barn.
Sinnes often knows the names of the sheep and puts their name and the farm they’re from on the label. She also lists the natural plants she uses to dye the wool. “There’s a sense of connection and transparency about where everything is coming from,” Sinnes says. “Sincere Sheep was born out of this.”
Sinnes teaches classes in natural dyeing at her Napa Valley studio as well as Fiber Circle Studio in Petaluma. “We happen to live in a place where we can grow or forage for a lot of dye plants, so we’re very lucky that way,” she says.
She grows indigo for blue colors and a few varieties of marigolds for warm golden yellows. She grows weld for a clear highlighter color of yellow. “I have foraged for oak galls and those give tans and grays,” she says. “I have also foraged for fennel and Queen Anne’s Lace which both give yellows.”
Sinnes also buys a lot of flowers from local farmers to use as dyes. “They’re agricultural products which support families and communities,” she says. “Synthetic dyes are made in a laboratory and they can be made from petroleum byproducts. These dyes begin on a farm.”
She says she joined Fibershed because it seemed sort of silly not to. “There was an alignment with what I was already doing,” she says.
Sinnes has seen an awareness among North Bay consumers who are avoiding synthetic fibers because of the large role they play in the release of microplastics. “In general, people who are interested in supporting their local farmers and things like natural dyes are going to be more interested in only working with natural fibers,” she says.
She notes that it was hard to point to any trends in sales because of the changes brought on by the pandemic. “That changed our being able to really track sales in a normal way,” she says. “We’re all trying to figure out what the new normal is. But in terms of the awareness and education level of the consumer, I think there’s absolutely an increase around all that.”
A fantastic fiber
Marlie de Swart closed Black Mountain Artisans in Point Reyes Station last year when the rent became too high. She had run the popular fiber artisan cooperative for 25 years. The core group of artisan spinners and knitters are still doing shows and open studios together.
She had hosted a popular knit group at the cooperative. “Anyone could come in and learn to knit or get help with knitting from the group,” she says. “It was both young people and older people. It was very nice.”
De Swart got involved with Fibershed when the organization first formed and was the first person to join its board of directors. “I totally believe in what Fibershed is doing, promoting local wool and trying to set up a wool industry, rather than have it thrown away,” she says.
De Swart was approached at the cooperative by local wool producers who were struggling with what to do with it. “Local farmers would come to the store and say, ‘I’ve got all this wool, but I can’t sell it, I can’t do anything with it,’” de Swart says. “I would say, well I spin and dye wool, so I’d love to have it.”
She sold yarn from the wool in the store and used it in her own creations. “So that’s how I created Bo-Rage Yarns and Designs,” de Swart says of her studio. “Bolinas is where I live and borage is a little blue flower that is very prevalent in my garden. So it made sense to name it that way. It’s all local. It’s from local farmers and local animals.”
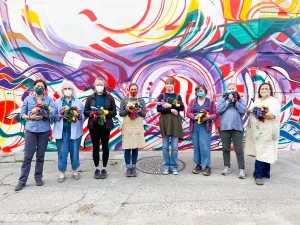
She loves wool and says it has the most wonderful properties. “It insulates, it sheds water, it stretches,” she says. “Overall, it’s a fantastic fiber. And as a craftsman, I’m sorry but working with wool is so much nicer than working with any synthetic fiber you can buy.”
De Swart understands the intrinsic value of wool from a childhood spent in Holland with its cold winters. She says the term “wicking” is a marketing term created to sell products to outdoor enthusiasts when in fact wool has its own way of keeping the body comfortable while we’re sweating.
De Swart says that most of the yarn she used to sell in the store she now uses in her own work. “Since the store closed I have started to weave again,” she says. “I got a new floor loom and I’m very involved with that now.” She dyes some of her wool and leaves some with their natural color.
De Swart has also created a book, Knitting Woolscapes: Designs inspired by Coastal Marin Wool. It’s a pattern book for hand knitters and contains 25 of her original designs, mostly sweaters.
The book has been a hit. De Swart notes that everything in the book is local. “The wool used came from local sheep, the models are local, the photographer, the page designer, the person doing layout, it’s all local.”
“When I had the store, more and more people were interested in the fact that things were made locally and that they were from local sheep,” she says. “Especially the younger generation, which to me was very encouraging to see that they are interested.”
De Swart points out that Fibershed is a youthful organization. “They’re younger—well younger than me obviously,” she says. “It’s quite remarkable what they have done and the awareness they have created. They will change the world, I think.”